Driving up the access road to Ravensdowns’ Lime quarry in Geraldine, felt more of pleasurable scenic drive, than a work field trip. Arriving at the quarry offices you are treated to vast 360 degree views of the Canterbury plains and surrounding forest clad hills and distant mountains of McKenzie country.
Sitting 220 metres above sea level the quarry has been in operation for over 40 years, with Ravensdown at the helm for the past 13 years. The lime quarry produces Ag Lime and track rock for the local rural market, producing over 100,000 tonnes of product annually. The production is reliant on the all Volvo fleet of machines which are used for extraction, breaking, stockpiling and loading to name a few of the many tasks the machines perform.
The fleet consists of two L150G wheel loaders, an EC240CL excavator which is used for rock breaking and loading the primary crusher, an EC380DL excavator, which is used for removing overburden and general duties and an A40E articulated hauler. Along with the Volvos’ the quarry operate a mobile primary impact crusher and a fixed tertiary crusher and processing plant.
We were greeted by the Quarry Manager Paul Johnston, who kindly began to give us a fascinating tour around the busy quarry, the working machines and production plant and his team.
Including Paul there are a team of seven operating the quarry. As soon as we stepped out of the door one of the local fert spreader trucks pulled up into the despatch area and one of the quarries L150G wheel loaders stepped into action to load the visiting truck full of Ag Lime. Heading up the hill further into the quarry we watched the EC240CL performing rock breaking duties and the EC380DL loading the A40E dump truck.
I was given the opportunity to talk to the two excavator operators first hand, about their thoughts and experiences of the Volvo machines. I was advised by them that the excavators were “Good all round”, especially the comfort of the machines and the user friendly set up providing a quality working environment with no operator fatigue. The double grouser set up on the EC380D offers very good stability around the lime site and the remote mounted greasing points allows the operators to grease everything on the machine without needing to move the boom, a handy time saving feature.
“We have seen a dramatically reduced fuel burn on all machines since becoming an all Volvo fleet site and also a reduction in Repair and Maintenance costs”, Paul commented.
He also advised that production rates were being maintained using the 38tonne Volvo excavator as a replacement to the previous 50tonne machine and burning less than half the amount of fuel.
The Volvo fleet are all monitored using the Volvo Caretrack system and the Matris readings are constantly analysed and used to understand the machines performance and operating costs. This tool will continue to be used in order to establish plant replacement strategies in the future and monitor machine health.
It was a pleasure to watch the machines in action in this breath-taking location. The manager and operators all appeared to be very proud of their Volvo fleet and quarry which was evident in both the presentation of the machines and in the highly organised, smooth production of the quarry.
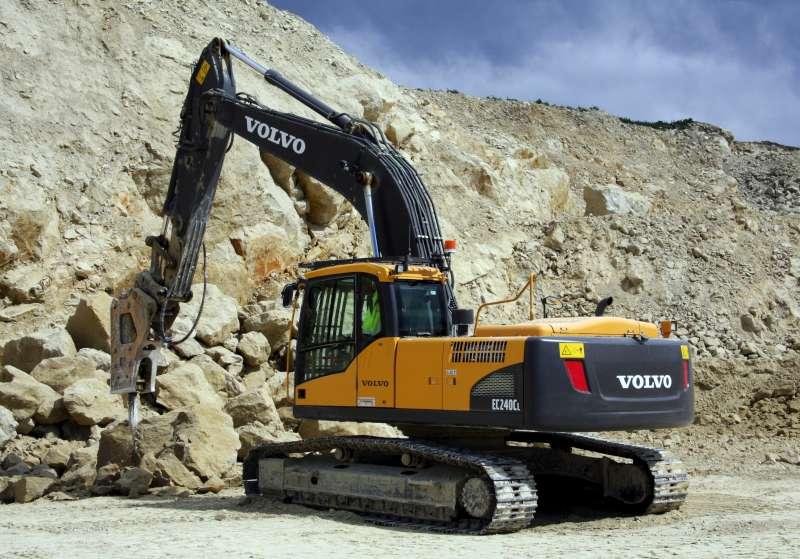
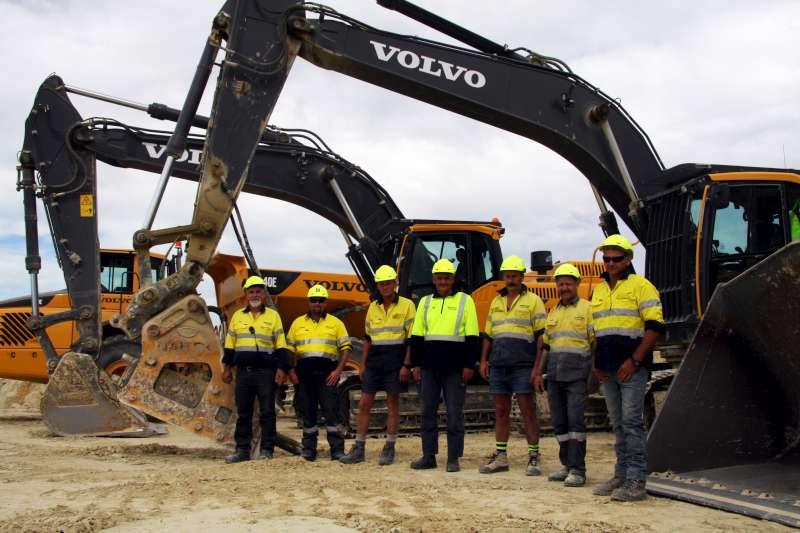
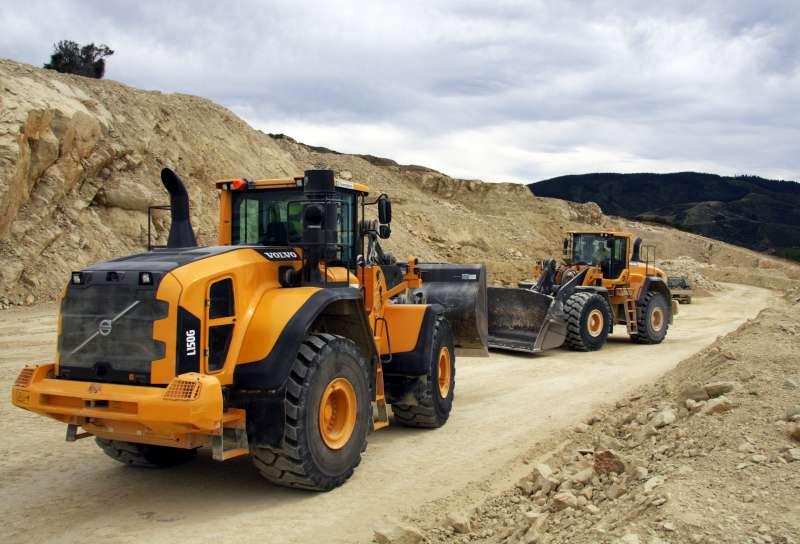
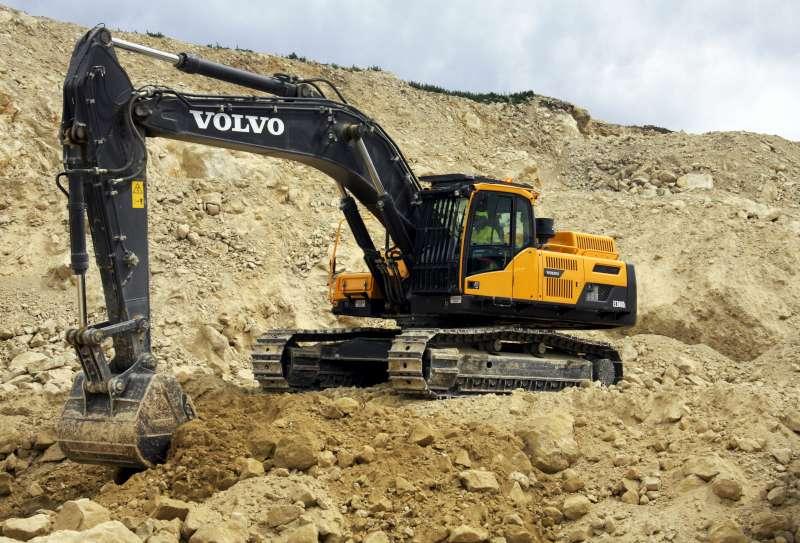
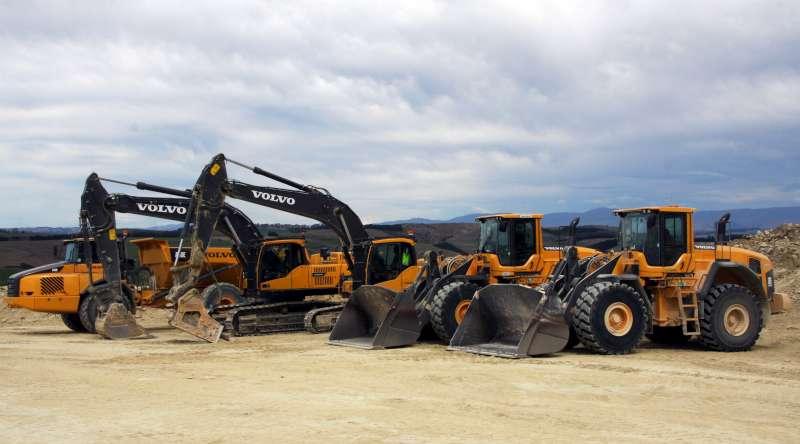
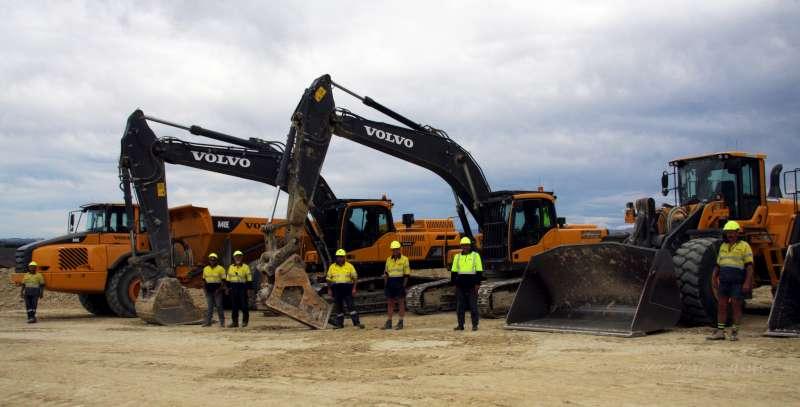
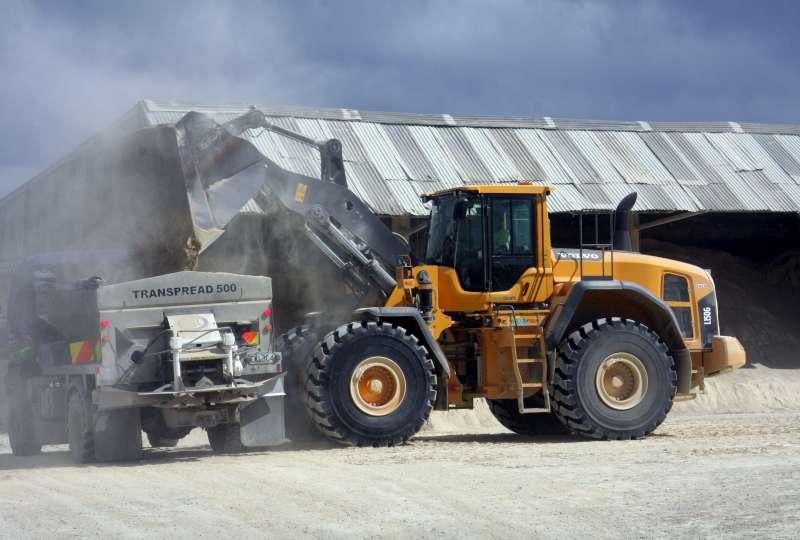
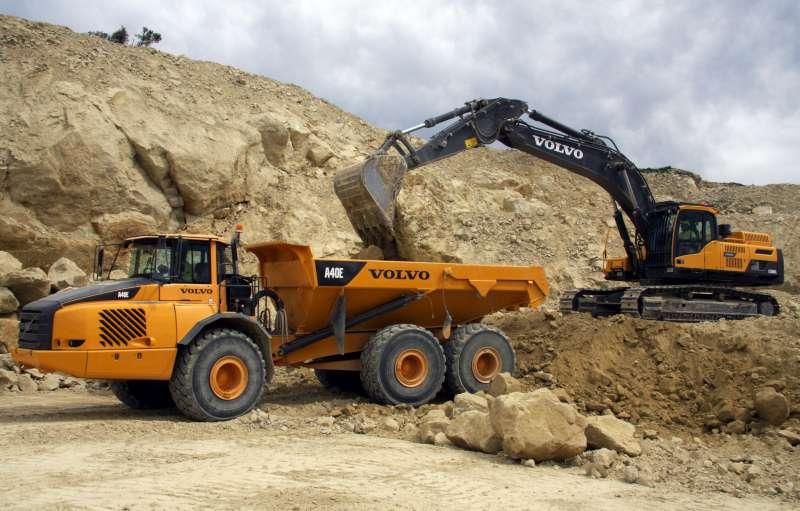